When it comes to welding and fabrication, choosing the right material can make all the difference in your project’s durability, appearance, and performance. Two popular options—stainless steel and mild steel—each bring unique characteristics to the table, and understanding their properties is crucial for making an informed decision.
Understanding the Basics
Let’s start with a common misconception: stainless steel means exactly what it says—it stains less than traditional steel. However, this doesn’t mean it’s completely impervious to corrosion. Stainless steel will still rust under certain conditions but significantly less than mild steel, thanks to its unique composition.
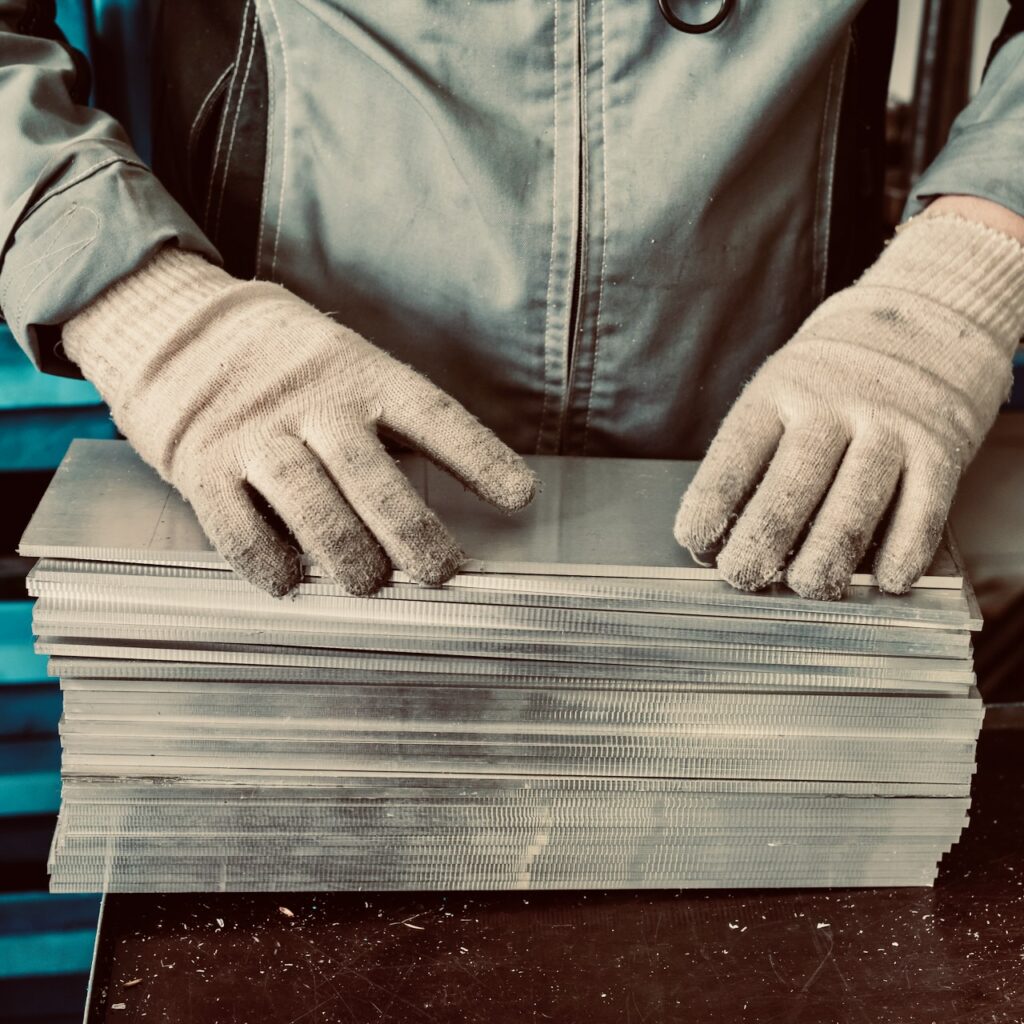
Environmental Corrosion Factors
Corrosion is heavily influenced by environmental conditions. The closer you are to the ocean, the more rapidly metal will rust. The same principle applies to:
- Humid environments
- Areas with high chlorine exposure
- Regions with frequent moisture and salt in the air
Visual Deception: Not All That Glitters is Stainless
An interesting phenomenon many people encounter is seeing seemingly rust-free metal surfaces that appear to be stainless steel. Often, these are actually:
- Chrome-plated surfaces
- Pacified and etched metal
- Surfaces with special protective treatments
These treatments can create a shiny, corrosion-resistant appearance that mimics stainless steel but isn’t actually stainless steel at its core.
Mild Steel: The Traditional Workhorse
Mild steel, also known as carbon steel, has been the backbone of industrial fabrication for decades. It’s affordable, easy to work with, and provides excellent strength for many applications. However, its Achilles’ heel is corrosion resistance. When exposed to moisture and oxygen, mild steel quickly develops rust, which can compromise the structural integrity of a project.
Stainless Steel: The Corrosion-Resistant Champion
Stainless steel contains chromium (at least 10.5%), which forms a thin protective layer of chromium oxide when exposed to oxygen. This passive layer is what gives stainless steel its remarkable resistance to staining and corrosion. The more chromium in the alloy, the better the corrosion resistance.
Welding Considerations
Mild Steel Welding
- Easier to weld
- Lower cost of materials
- Requires additional protective coatings to prevent rust
- Ideal for indoor projects or those with minimal moisture exposure
Stainless Steel Welding
- More complex welding process
- Higher material costs
- Requires specialized welding techniques
- Better for projects exposed to corrosive environments
- Multiple grades available for different applications
Pros and Cons Breakdown
Mild Steel
Pros:
- Lower cost
- Easy to form and shape
- High tensile strength
- Simple to weld
Cons:
- Prone to corrosion
- Requires regular maintenance
- Limited use in harsh environments
- Rapid deterioration in maritime or humid conditions
Stainless Steel
Pros:
- Excellent corrosion resistance
- Long-term durability
- Aesthetic appeal
- Hygienic properties
- Better performance in challenging environments
Cons:
- Higher initial cost
- More challenging to weld
- Slightly lower strength compared to some mild steel grades
Choosing the Right Material
Your choice between stainless steel and mild steel depends on several factors:
- Project Environment: Consider exposure to moisture, chemicals, or salt.
- Budget Constraints: Mild steel is more affordable initially.
- Aesthetic Requirements: Stainless steel’s finish is visually appealing.
- Long-Term Maintenance Expectations: Stainless steel requires less maintenance.
- Proximity to Corrosive Elements: Areas near oceans or chlorine-rich environments benefit from stainless steel.
Practical Tips for Welders
- Don’t be fooled by surface treatments that mimic stainless steel.
- For indoor, dry environments, mild steel is often sufficient.
- In marine or chemical environments, invest in stainless steel.
- Consider the total lifecycle cost, not just initial material expenses.
- Use appropriate welding techniques specific to each material.
- Be aware of environmental factors that accelerate corrosion.
While stainless steel might cost more upfront, its long-term benefits often outweigh the initial investment. Understanding the nuanced differences between these materials empowers welders and fabricators to make informed decisions that balance performance, durability, and cost-effectiveness.
Remember, no material is perfect for every situation. Carefully assess your project’s specific requirements, especially environmental conditions, to select the most appropriate steel type.
Contact us today to learn how we can assist with your structural welding needs!
At J&M Welding Inc., we bring decades of experience, certified expertise, and unwavering commitment to quality to every welding project. Contact us to learn how we can help ensure the success and longevity of your next construction project.